How to Pick the Right Acme Nut for Your Next Lead Screw Application!
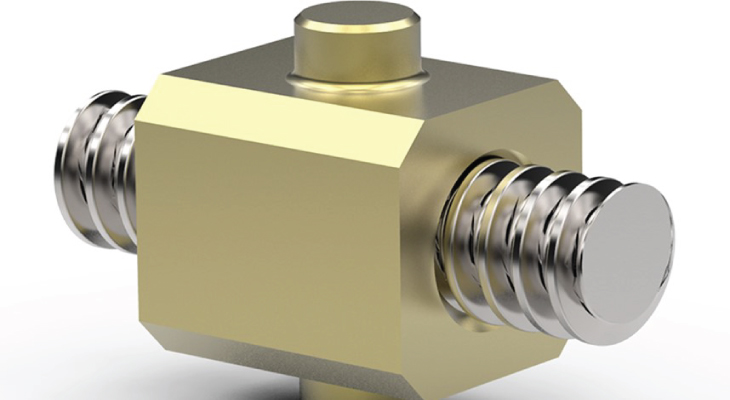
High-end, motion control lead screw applications only perform as anticipated when the screw is matched with the proper acme nut—whether the acme nut is available as a standard component or produced from a specific custom design.
Many of today’s more challenging motion control applications, such as those used in lab automation and medical treatment devices, require precise linear motion control yet are not conducive to using traditional ball screws because of noise, space, cost, and lubrication concerns. Instead, engineers turn to advanced screw technologies, utilizing custom-made acme nuts and specially engineered lead and acme screw innovations.
To assess whether available acme nut options will meet the needs of your application or if you need a custom-engineered acme nut, you need to evaluate how the unique characteristics of your design match up with acme nut features, options, and capabilities.
Design variables to consider
Begin by evaluating essential variables in your design, including:
- Temperature constraints – Does your device need to operate within a specific temperature range?
- Chemical compatibility – Are there certain materials that your environment will negatively impact, or is corrosion resistance important?
- Wear factor – How long must your acme nut and screw operate before it wears out and needs to be replaced?
- Matching leads – Do the leads in your acme screws all have to match?
- Maintenance – Have you included access to your linear motion assembly for maintenance purposes?
- Lubrication – Can you use traditional lubricants, or do you need a special lubrication coating like PTFE for your applications?
- Backlash – Is backlash a concern?
- Flange or no flange – Which approach works better in your design?
Acme nut features and options
After evaluating your design variables, compare those needs against standard acme nut features or options to determine if they fit. If not, your lead screw application may require a custom-engineered lead nut for a more tailored, specific solution. Acme nut options and features to consider include:
- Compactness
- Dynamic Load Capacity
- Minimal Drag Torque
- Vibration Dampening
- Smoothness of Operation
- Backlash/Wear Compensation
- Stiffness
- Lead Capability
Helix acme nut customization will exceed your expectations.
For more than 40 years, Helix Linear Technologies engineers have produced standard and customized acme nut designs that surpass industry expectations. To meet new market demands for innovative products and applications, Helix customers often need to customize their acme nuts within their lead screw applications to boost productivity, efficiency, and precision.
Helix offers a wide variety of standard acme nut designs that provide the features and options required for many precision acme screw applications. If your specifications don’t match any of the acme nut products, features, and options, Helix can engineer a customized acme nut that fits your application requirements perfectly. Customized acme nuts may involve simple dimensional changes, unique materials, different mounting hole patterns, specific thread options, or production techniques.
Helix has capabilities for molding and machining a complete array of acme nuts and other actuator components from a range of materials, including standard polymers, such as PEEK, Torlon®, Acetal, Polypropylene, Turcite®, as well as from custom-engineered polymers, including acme nut PTFE, PFPE, silicone, carbon fibers, graphite, glass fibers, and molybdenum disulfide.
Should cost or design constraints require a more integrated package, the Helix engineering staff can help you simplify your design by combining several different components into a molded nut. Helix manufactures precision acme screws by thread rolling, thread milling, or thread grinding processes. Helix acme nuts and lead screws provide the precision and flexibility critical to many of today’s motion control requirements.